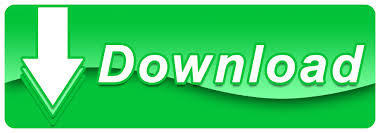
Compression forming provides forging flow in multiple or customized directions. Upset forging increases the width of the products and decreases length. This broad range of processes can be grouped into three primary umbrella groups: Image credit: /Aumm graphixphoto What are the different forging processes?īeyond basic hot and cold forging, many specific processes exist. Hot forging being used to create automotive parts.
#List of forging die design handbook full#
and Canada.įor more detailed info on either of these processes please read our Full Guide to Hot Forging and Cold Forging. Need a cold forging company? Thomas' Supplier Discovery has a vetted list of Cold Forging Companies in the U.S. However, this increased versatility comes at a cost, because cold forging requires more powerful equipment and may call for the use of intermediate anneals. Cold forging encompasses numerous forging techniques, including bending, extruding, cold drawing, coining, and cold heading. Despite this hindrance, cold forging does edge out its warmer equivalent when it comes to standards of dimensional control, product uniformity, surface finish, and contamination. Many metals, such as steel high in carbon, are simply too strong for cold forging. Cold ForgingĬold forging typically refers to forging a metal at room temperature, though any temperature below recrystallization is possible. Need a hot forging company? Thomas' Supplier Discovery has a vetted list of Hot Forging Companies in the U.S. Hot forged products also benefit from the elimination of chemical inconsistencies. This is because excessive heat decreases yield strength and improves ductility. The main benefit of hot forging is the decrease in energy required to form the metal properly. This can mean heating metals up to 2,300 degrees Fahrenheit. Hot forging requires the metal to be heated above its recrystallization temperature. Once the forging tools have been created, products can be manufactured at relatively high speeds with minimal downtime.There are two main types of forging: hot and cold. Another advantage of forging is the relatively low costs associated with moderate and long production runs. Ancillary effects of this unique grain flow include the elimination of defects, inclusions, and porosity in the product. This causes the metal to retain its strength. The pounding action of forging deforms and shapes the metal, which results in unbroken grain flow. Forging is also used to fortify hand tools such as chisels, rivets, screws, and bolts. It is used to produce critical aircraft parts and transportation equipment. The forging process is highly multipurpose and can be used on small parts just a few inches in size to large components that weigh up to 700,000 lbs. Through forging, a favorable grain structure can be created, making the forged metal sturdier. While impurities should be managed during the initial casting process, forging further refines the metal.Īnother way that forging strengthens metal is by alternating its grain structure, which is the metal material's grain flow as it deforms. Inclusions are compound materials implanted inside steel throughout manufacturing that cause stress points in the final forged parts. This vastly reduces inclusions in the forged part. The hot forging process also breaks up impurities in the metal and redistributes such material across the metalwork. As metal is heated and pressed, minor cracks are sealed, and any empty spaces in the metal close. Compared to other manufacturing methods, metal forging produces some of the sturdiest manufactured parts available. The purpose of forging is to create metal parts. Image credit: /Drpixel What is the purpose of forging? A traditional hammer and anvil are used for forging.


Some of the common materials used for forging are carbon steel, alloy steel, microalloy steel, stainless steel, aluminum, and titanium. This is because today, forging is most commonly performed with the use of forging presses or hammering tools that are powered by electricity, hydraulics or compressed air. Since its origins in the fertile crescent, forging has experienced significant changes, resulting in a more efficient, faster, and more durable process. Forging, a metal shaping technique using compressive, localized forces, has been a staple metal fabrication technique since the time of the ancient Mesopotamians.
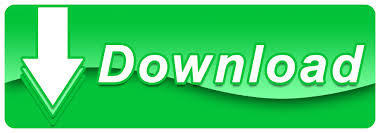